+
Product Features
For processing copper, aluminum, zinc and lead metallic products
- Assured operating safety and longer service life of console due to excellent rigid structure of the entire unit with safety coefficient at folds of theoretical figure, assurance of operation.
- Reinforced design and treatment to all linkage structure, chucks heat and chemically treated to give better molding, bending and corrosion resistance, safe and longer service life.
- Man-machine friendly structure of the control to minimize the operation range with the layout of all systems designed for easier manual adjustment and visual inspection.
- 2-door frame configuration for firmly secured console, significant reduction of jolting and vibration during operation due to higher gravity, also reducing consonance with door frame configuration design, preventing loosen parts and increasing the stability of the entire console.
- Oil hydraulic system control pooling mechanism to concentrate all oil hydraulic control parts and gate valves on the total control panel located at the mid of the console for easier control of the entire unit, adjustment options and changes as required.
- Voluntary flow oil pipeline designed with the oil inlet of pump at a level lower than that of the oil tank, no-load type of pressure valve adopted with super mute oil hydraulic pump and dual-pressure storage design oil path for quite and fast operation to save power consumption and to deliver reliable and consistent oil pressure.
- Mold opening and closing modes allow options
of high/low pressure, cycle of fast/slow rate
or inertial control, trouble-free mould
locking, upgraded operation efficiency, better
control of moulds closing than any
conventional art, and providing longer service
life.
- Lateral safety gate, with guard adjustable,
enclosed type of protection for fear-free
operation to the operator.
- Additional to the conventional top extrusion
method, updated multi-sectional dual-hydraulic
cylinders extrusion system from top downward
is provided allowing top and bottom extrusion
options to increase the functional flexibility
of the console.
- Oil pipeline designed with embedded piping
for improved operational safety, and easy and
safety cleaning and maintenance routines.
- Injection oil cylinder fixture integrated
with fixation panel for larger contact area,
more reliable and precision injection.
- Cooling system for injection piston to
significantly prolong the plug service life,
ingenious structure design to permit easier
and agile (dis) mounting of the piston.
- Auto-lubricating system depending on the
frequency of mold closing with oil delivered
at consistent pressure at each lubrication
point for assured lubrication results.
- Oiling mechanism with specially designed oil
groove, filler and bath to make easier the
lubricating for all sliding or revolving
mechanism.
- Console wall made of high density FCD,
sturdy, and incorporated with special
treatment of the motion structure to come up
with a fortress like mechanism
configuration.
- Fast and precise (dis) mounting of mould
positioning plate, injection pipes of mold
calibration, center of injection inlet and
molds.
- Four sideway fenders additionally provided
to the configuration for the base and fixation
plate for improved stability and rigidity of
the base, preventing accidental collision to
minimize the damage to the peripheral parts or
the base configuration.
- Mold opening and closing adjustable,
provided with buffer device to allow
instantaneous start and stop of the oil
cylinder, thus smooth and well-facilitated
operation.
- Diversified options by electronically
controlled parts to select standard limiting
SW control or linear rule, or translator
adjustment/calibration control location for
operation (optional).
- Adjustable oil seal design, made of highly
heat withstanding, wearing proof oil seal and
low friction coefficient Teflon ® rings to
ensure effective output and longer service
life of the oil cylinder.
- Multi-sectional selection of injection
control to upgrade quality of the castings,
and overcome blind point on mold for any type
of product.
- Spacing adjusting safety control to suspend
the injection in case of improper closing of
the molds or insufficient pressure for locking
up the molds for integrated concerns of
operational safety.
- Kiln made of heat insulation and refractory
materials to upgrade thermal efficiency,
energy saving and faster heating.
- Auto temperature control and 24H ignition
control devices, to save the length manual
start-up while securing the control of
consistent temperature.
- High-load and inverse operation tests to
assure of excellent performance by each
control elements, with parts imported from
leading genuine makers.
- Unique design for oil spray, air spray, gas heating, cooling system, etc. controllable at the central panel for easy and convenient control by the operator, in conjunction with handy design of the peripherals to outperform any equivalent models from other makers.
- Diversified optional equipments with each giving superb functions including automatic ladle, extractor, sprayer, dual safety door, optical sensor safety control, safety hook to prevent accidental fall, and many others for care free operation by the owner.
PLC has been already a popular standard power machine control mechanism, and we have developed PC-100 grade advanced digital touch screen control optional equipment to double the memory capacity of the module. (Optional)
|
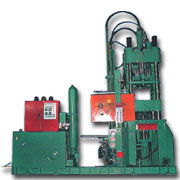
CF-150SM
- Specification
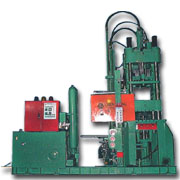
CF-250SM -Specification
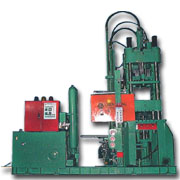
CF-350SM - Specification
CF-500SM
- Specification
CF-1000SM
- Specification
|